Getting on the front foot with risk management
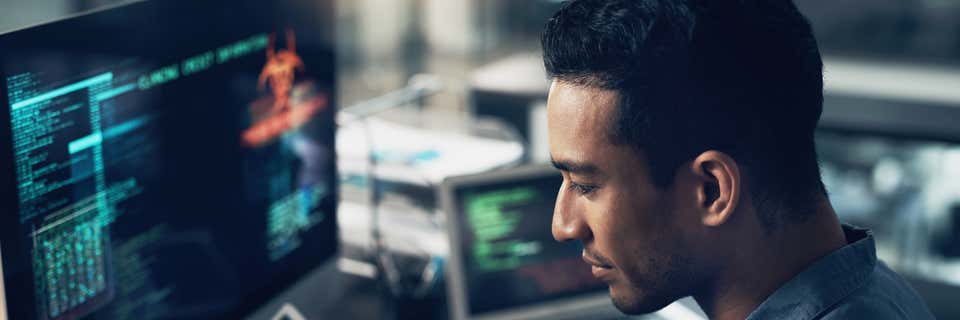
- Blog
September 15, 2022 |
8 min read
- Blog
What’s the risk involved with the shoes we put on our feet?
In the second blog post with a Clarks shoes employee recently certified in Management of Risk (M_o_R 4), Materials Manager Polly Parr talks risk and mitigation when selecting what shoes are made of:
When manufacturing shoes, it’s important to make them cost-effectively. However, if shoes are generating returns from unhappy customers, that’s neither a well-designed nor well-costed product.
Therefore, it’s up to me to do the necessary due diligence and assess risk ahead of time.
As Materials Manager, my responsibility covers any type of upper or shoe lining in materials like suede, leather, recycled leather and non-leather. I need to ensure that all materials are fit for purpose and will avoid issues – such as strength and abrasion potential – that might create returns.
So, over a period of up to a couple of months, that can include wear tests and laboratory reports for any new materials.
Risk (and management of risk) in my role
For me, managing risk is about trying to mitigate what could happen down the line by putting in early tests analysis.
Our operating model means we allow the factories making our shoes to use a supplier of their choice, as long as the supplier has been through the Clarks approval and audit process and can produce a product to our specifications.
So where does risk come into it? One of the main issues relates to colour of materials: when we supply a swatch with the desired colour, there is often a risk that the supplier won’t match the colour exactly. A human checking process can lead to human error, with a knock-on risk for shops selling the shoes to customers.
Learnings from Management of Risk (M_o_R 4)
Today, businesses are in a world where it’s a constant battle against costs and maximising margins. So, studying and certifying in M_o_R 4 provides a range of different models to use when managing risk.
Having a best practice approach based on industry standards means I’ve got options for showing people who work outside my role how to categorise risk and therefore mitigate problems further along the production process.
By being five or more steps ahead helps to ensure the overall pathway isn’t blocked and is a better way to manage than having to go back into the process and clear the pathway of problems that have already happened.
Taking a forward-thinking approach to risk means planning in advance to minimise the chance of a risk becoming an issue. Essentially, this means short-term pain for long-term gain.
One example of this in my work is dealing with metallic foil materials and how they are attached to shoes. These have inbuilt risks that can brings unexpected problems to the manufacturing process. Therefore, managing this risk means creating a sample in one colour and running a wear test. As a result, we’re able to capture facts and figures from tests and lab reports for any new materials before deciding how to progress.
In managing risk with a best practice approach such as M_o_R 4, there’s an element of knowing that I’ve done all I could with information at the time, with evidence to back up that my decision was the right one. Therefore, I can prove I’ve done my due diligence.